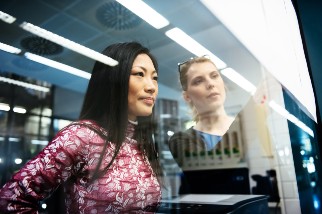
Inside a company’s organizational processes lie the root causes of many safety issues. To find and eliminate these issues, you must dive into process management.
Pete Susca, principal of OpX Safety, an expert in organizational process management and the author of more than 20 publications on the subject, recently led a webinar touching on a wide range of process management concepts that can help you gain leadership support for your initiatives, reduce risk and improve safety. The webinar was presented by our Healthcare Practice Specialty, Public Sector Practice Specialty and Blacks in Safety Excellence (BISE) Common Interest Group communities.
Susca lightheartedly calls his process management perspective “galactic safety,” a focus on strategies that go beyond technical safety and focus on organizational operations, processes and decision-making. Here are eight ways he believes you can use this process management mindset to change your organization.
1. See Safety Issues as Symptoms of Poor Decision-Making
“I want you to see safety issues as symptoms, not just as things to fix,” Susca says. “They’re messages; they’re little taps on the door. You need to open the door and walk through, not fix it and shut the door.”
When a safety issue arises, rather than merely treating the symptom, eliminate the root cause: decisions that happen upstream.
To follow the safety symptom back to the decision that produced it, look through 1) the risk itself; 2) processes and programs; 3) management systems; and 4) the organization’s culture. By considering the relationships among these elements, you can find the places where safety is not balanced with business goals, creating risk and leading to unwanted outcomes.
Leaders may understand that their decisions affect safety outcomes, but it’s often helpful to clarify the connections.
2. To Improve Safety, Improve Process Health
“Process health is the future of organizational common language,” Susca says. It’s where all functions of the organization can come together.
By taking an organizational process perspective, safety leaders can “get off safety island and start working with the people on the mainland and talking about healthy business.”
Susca uses process health to make a business case for new safety programs and initiatives.
“I don’t even make a business case for safety,” he says. “I make a business case for the fact that the process that created the safety risk is costing us money because it’s not a good business process. Make that business case and the cost of safety and hazard or exposure elimination comes along for the ride in the ROI.”
3. Determine What “Safe Enough” Means for Your Organization
One definition many organizational leaders don’t know — that safety professionals often assume they do — is what is “safe enough.”
Safety professionals know that there is no such thing as “zero risk” when it comes to safety, yet many haven’t helped their organization’s leaders define what “safe enough” means. Often, organizations state their goal is not to injure anyone. But how do you measure the potential for not injuring anyone, Susca asks.
Answering that question depends on the company’s values and it will guide how a company makes all its decisions around safety.
4. Develop Procedural Discipline
If an organization is not disciplined in following procedures, “every single imperative that is being managed by a procedure is at risk.”
When an organization doesn’t adhere to procedural discipline, employees know they can round the edges on procedures, whether they are simply standard operating procedures or life-and-death safety procedures.
5. Outline Roles and Responsibilities in Safety
Does your chief financial officer know their role in safety? Does your sales staff have safety responsibilities written into their job descriptions? Susca argues that every employee at an organization should understand those responsibilities.
Consider this scenario: A procurement officer decides to buy a 55-gallon drum of a liquid instead of many 5-gallon containers because it costs less. But when that drum is delivered, the site has no equipment to move it. The warehouse workers want to do a good job, so they figure out how to move it — at their own risk.
“That hazard was created by a procurement person who wasn’t balancing safety with cost,” Susca says. “Yet that is their job.”
Safety professionals must take three steps to rectify this situation: 1) Work with executive leadership and human resources to help clarify all workers’ roles in safety; 2) bring them data on risk value so they can make better decisions; and 3) give them the skills and tools needed to execute these decisions.
6. Reduce Unnecessary Front-Line Decision-Making
Most first-line supervisors “juggle too many balls” and have too many separate priorities. What happens?
“They’re juggling the thing that is on fire, that’s most important to them, that is most likely to get them in trouble,” Susca says. “There are balls rolling around on the floor, and they’re all at risk.”
To address this, organizations must clarify decisions being made at the top across all silos and learn how to reduce them through process efficiencies.
7. Value Process Health More Than Results
Create a common understanding and appreciation for process health – what it takes to make practical, value-integrated processes that work at the front-line of the organization.
This applies to every function (sales, purchasing, human resources, finance, etc.) as well as production and service. Assess the health, rather than the results, of processes to anticipate and mitigate risks.
8. To Create Better Processes, Think of Lego Instructions
The best processes follow simplistic principles, and there’s no process more simplistically communicated than Lego instructions, Susca says. They can be communicated, executed and checked entirely without words.
Creating simplified instructions reduces both risk and cost by creating more efficient processes that are easier to explain to new employees.
Whether you are redesigning processes into simple steps or clearly defining what your organization decides is safe enough, diving into these aspects of process management can ultimately help your company improve both safety and its bottom line.
Choose the Right Safety Management System
Get the resources and expert support you need to make informed decisions and drive results at your organization.
Learn more