When workplace injuries occur, they present employers with a choice. They can take a reactive approach, treat the worker’s injury and continue business as usual, or they can use it as a learning experience to improve their operation and prevent future injuries. 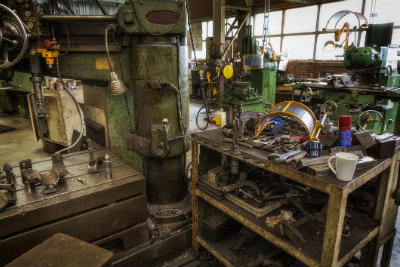
Following a workplace injury, Woods Hole Oceanographic institution (WHOI) chose to do the latter and developed a comprehensive machine shop safety program to proactively address the safety issues that existed in its 25 machine shops.
WHOI is a non-profit organization, based in Woods Hole, Massachusetts, dedicated to ocean research, exploration and education. Its machine shop personnel design, fabricate and maintain the ships, vehicles and facilities that WHOI uses to carry out its oceanographic work.
The incident in question took place in 2015. A machinist suffered serious hand lacerations while using a waterjet machine that cuts thick metal parts. The worker underwent emergency surgery and stayed overnight in the hospital. Investigation of the incident indicated that had the machinist’s hand been at a somewhat different angle, it would have been amputated.
In response to the incident, OSHA cited WHOI with a serious violation under 29 CFR 1910.212(s)(1) – General requirements for all machines. Its investigation found that the water jet machine was “not properly guarded to prevent workers from being injured by the water jet emanating from the nozzle.”
Furthermore, the injured machinist violated the operating procedure for the machine, which prohibits more than one user operating it at a time. When the incident occurred, the machinist and another operator were using the water jet machine, with one operator positioning the metal piece for cutting.
As a result of the OSHA citation, a pressure-sensing mat was installed in front of the water jet machine and employees were trained on the proper operating procedure. WHOI didn’t stop there, however, and used this incident as an opportunity to improve its operation through a comprehensive machine shop safety program.
Prior to this incident and the subsequent OSHA citation, WHOI’s safety program consisted of an online machine shop training module and a one-page shop safety rules document that was posted in all machine shops.
The first step in the process was conducting an inventory and inspecting all machinery in each machine shop, and documented the personnel using it. A senior consultant was hired to inspect each machine shop as well. The inspection determined that the most frequently identified opportunity for improvement was in machine guarding. Several machines at WHOI’s campuses were older and did not have adequate safeguards in place.
WHOI decided that any machines without proper safeguarding would be locked out of service until suitable controls were installed. Furthermore, they would dispose of any machines that were cost-prohibitive to repair.
From there, WHOI developed a three-tier classification system to categorize machinery in terms of the hazards it presents.
Class 1: Low-hazard machinery such as a belt sander, circular saw or router. Class 1 machine operators must have permission from the machine shop owner to use the machinery.
Class 2: Medium-hazard machinery including a full-size band saw, full-size drill press, water jet or bench grinder. Class 2 machinery operators must be certified by the shop supervisor as an authorized operator, which includes machine-specific training.
Class 3: Most-hazardous machinery, such as full-size milling machines and lathes, and table saws not equipped with SawStop safety technology or equivalent. Class 3 machinery operators must be certified as authorized operators by the shop supervisor, which includes machine-specific training. In addition, a shop supervisor must be present during operation of any class 3 machinery.
As part of the program’s implementation, WHOI requires operators of all machinery classifications to initially complete the online machine shop safety training, and subsequently every two years.
Moving beyond machinery-related hazards, WHOI knew that the safety program must also establish roles and responsibilities for the different personnel in the machine shops, including provisions for which personnel have access to different types of machinery. Given the nature of WHOI’s operation, with 23 satellite machine shops used by research personnel, it was necessary to prevent unauthorized users from accessing machinery.
In addition, non-machinery-related hazards needed to be addressed, and machinists had to be educated on proper operating procedures for various machines. WHOI identified six key elements that, along with the machine hazard classification system, are the foundation of the safety management program.
1. Roles, responsibilities and authorization process
Many departments were involved in the development of the safety management program and, as such, are responsible for its implementation. The program identifies responsibilities for each departments and its role in safety management:
- Environmental health and safety (EH&S) department. Oversees the safety program, including the machine shop safety guideline and online machine shop safety training. In addition, the EH&S department conducts incident investigations and annual safety inspections. The goal of safety inspections is to identify and correct hazardous conditions. Incident investigations identify the cause of incidents so that personnel can learn from the experience and prevent incidents from recurring.
- Facilities department. Approves class 2 and 3 shop supervisors, which may involve vetting of candidates by professional machinists in the facilities department. Candidates must demonstrate that they can safely use the machinery that they will oversee and review oversight responsibilities for a class 2 or 3 machine shop. The facilities department also assists with maintenance of machine shops and machinery.
- Machine shop supervisors. Oversee all aspects of the machine shops, including maintenance, machine-specific training, controlling access to hazardous machinery, implementing safety guidelines and approving authorized operators. Machine shop supervisors must also approve and maintain a list of authorized supervisors for each class 2 or class 3 machine. In addition, they must be familiar and experienced with the safe operation of all machinery, equipment and tools in the machine shop, and meet the definition of a competent person.
- Authorized operators. May only use the machinery that they have been certified to operate by the shop supervisor and must follow all shop safety requirements. Before being certified as an authorized user, prospective class 2 or 3 operators must demonstrate the safe use of the machinery that they will be operating and have an understanding of shop safety rules.
2. Machinery maintenance and hazard controls
For a safety program to be truly effective, machines must be periodically inspected and evaluated to ensure they are in proper working order. As such, WHOI’s program states that shop supervisors and authorized operators are responsible for seeing that machinery is maintained and that any machinery deemed unsafe to operate is immediately locked and tagged out of service.
As an added measure to prevent unauthorized users from operating class 3 machinery, WHOI equipped class 3 power supplies with key-operated selector switches. The keys for these switches are issued only to class 3 shop supervisors and authorized operators.
3. Shop safety rules and PPE
To ensure that everyone understands proper safety procedures, WHOI posts safety rules in each machine shop that have been reviewed and signed by all authorized operators of class 2 and class 3 machinery. In addition, the shop supervisor’s name and contact number is posted at each machine shop entrance, along with a notice that states that only trained and authorized personnel may operate machinery.
All personnel working in the machine shop must, at minimum, wear safety googles and closed-toe shoes. Shop supervisors are required to conduct a hazard analysis of the operations within their particular machine shop to determine the need for any additional PPE such as eye and face protection, head protection, hearing protection or protective gloves.
4. Fire prevention
As with many work sites, WHOI machine shops contain hazards related to fire and combustible materials. So, the organization’s program includes a combustible dust safety procedure, which defines combustible dust as any finely divided solid material that presents a fire or explosion hazard when dispersed and ignited in air. To prevent incidents involving combustible dust, machine shop personnel must must remove combustible dust residue from shop surfaces so that no more than 3 mm of dust accumulates.
To address other fire hazards such as hot work or oily rags, the safety program requires that hot work be conducted in authorized, controlled areas or under a hot-work permit, and that oily rags are collected and deposited into approved steel waste cans with self-closing lids.
In the event of a fire, all machine shops are equipped with sprinkler systems and either Class ABC portable fire extinguishers, or Class D portable fire extinguishers in the case of larger machine shops that generate large quantities of metal shavings and turnings.
5. Shop inspections and reporting
As noted, one way that WHOI identifies and corrects hazards is through annual safety inspections. THE EH&S department conducts these inspections, prioritizing hazards as either an immediate hazard, a safety requirement or a best management practice. Immediate hazards must be corrected right away, safety requirements within 30 days and best management practices are optional.
From there, corrective actions are identified for each hazard and assigned to an individual in the machine shop. The EH&S department then tracks the progress of each action through completion. Shop supervisors must conduct inspections on their machine shops either daily or before using machinery to ensure that they are in compliance with shop safety requirements.
When incidents and near-hits occur, they are reported by those involved in the incident or their supervisor. Going beyond traditional reporting, not only is the incident itself described, but contributing causes and preventive methods are also documented. All incidents and near-hits are investigated by the EH&S department to verify what occurred, why it occurred and how it can be avoided in the future.
6. Waste management
Recognizing the role that waste can play in creating hazardous situations, waste management plays an important role in WHOI’s program. Waste management is overseen by the EH&S department, which conducts training on topics such as recycling, hazardous waste management and waste minimization.
After each shift, waste metals such as aluminum, titanium and stainless steel are separated by type and collected for recycling. Chemical products used in the machine shops that result in regulated waste streams, (those defined as hazardous waste by the Massachusetts Department of Environmental Protection) are also separated by type and collected in satellite accumulation areas.
Since the implementation of the machine shop safety program, WHOI has had no OSHA-recordable injuries or illnesses as a result of working with machinery in its machine shops.
The work that WHOI has done to improve its operation is just one example of how to use incidents and near-hits as a way to learn about the hazards associated with its operation so that they can be prevented moving forward. By taking a proactive approach and continually examining the effectiveness of safeguards and controls used to protect employee safety, organizations can establish a sustained record of safety improvement.
Read the complete version of “Machine Shop Safety: A Look at the Woods Hole Oceanographic Institution Program,” originally published in the April 2018 issue of Professional Safety.
Choose the Right Safety Management System
We have the resources and expert support you need to make informed decisions and drive results at your organization.