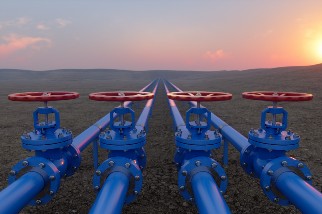
When things go wrong with natural gas and fired equipment, they often go very wrong.
John Puskar, P.E., president of engineering consultancy Prescient Technical Services, has served as a forensic expert on some of the worst fuel and combustion equipment disasters in history. In a recent webinar, presented by our Fire Protection member community, he highlighted natural gas and fired equipment workplace incidents that led to equipment rocketing through roofs leading to fatalities, gas leaks that caused mass evacuations and hospitalizations, and fiery explosions that cost billions in damages.
Most of these catastrophic incidents were preceded by subtle signs or small procedural problems, Puskar says. Based on 40 years experience as a licensed engineer and service on multiple national code committees, Puskar points to five common natural gas and fired equipment hazards that you need to understand.
Hazard 1: Not Understanding All Three Ways to Turn Off the Gas
Turning off the gas at your facility is not always as straightforward as it may seem. While safety professionals do “an excellent job” of getting to a zero-energy state and having lockout/tagout procedures for electrical systems, many don’t do the same with fuel gasses, Puskar says.
That’s why having a clear plan to shut off gas is key. In most facilities, this is done in one of three ways. This checklist can get you started (and you can see all three with visuals and further detail in Puskar’s webinar).
1. The main gas shut-off by the utility meter.
- Answer essential questions. Where is the main shut-off valve? How do you access it? How can you tell if the valve is open or closed? Is this information marked in some way? How do you operate it (is there a handle, do you need a pipe wrench, etc.)? Is the gas/utility emergency phone number on it? What do you do after you shut off the gas?
- Know the location of the custody transfer line. Contact the utility to determine the exact demarcation point. If the main shut-off is in a fenced-in, utility-equipment, non-access area, do you have access and how is this marked?
- Check your valve. The National Fire Protection Association’s National Fuel Gas Code (NFPA 54) requires that customers provide their own valve. Do not assume there is a valve available to use. If you see a utilities valve, it might have a pin lock on it, which would make it inoperable. It might also require a special handle.
2. A remote, accessible, manual shut-off valve, as required by NFPA 86 for all fired equipment (other than boilers).
- Prepare to respond to incidents. If there were an explosion or a fire were in progress, would you have an accessible valve?
3. The equipment shut-off isolation valve.
- Know where to look. This is usually the valve at the beginning of the fuel train, before the regulator. These must be lockable, quarter-turn valves with fixed handles.
Take time to consider how you would not only isolate or shut off the natural gas, but also purge the system to work on it. New requirements in NFPA 54 require that systems be designed and installed to accommodate purging.
With any of these methods, you may encounter lubricated plug valves, which Puskar says are in service in more than 50% of all natural gas piping installations. Pay close attention to these valves, which must be serviced, often annually. It’s likely you will encounter some that have never been serviced, he adds.
Basic plug valve issues have contributed to major, fatal incidents, like a 1999 explosion at the Ford Motor Company Rouge River complex that occurred, in part, because a plug valve was open and required considerable force to operate. When these valves are not serviced as required, they can become seized in position and stop functioning.
Hazard 2: Forgetting the Signs of Carbon Monoxide Are Subtle
Because carbon monoxide (CO) is odorless and tasteless, our senses can’t detect it. However, Puskar says safety professionals should educate workers on two “subtle” signs:
- The combustion process that makes CO often makes other elements known as “surrogate indicators” of CO, including alcohol, ammonia formaldehyde and carbon. These are not odorless and tasteless, and may cause sinus irritation and watering eyes.
- Flames can also reveal a CO issue with their color, shape, symmetry and burner damage.
Furthermore, it’s important to remember that it can take up to 5 minutes to establish a draft. To be compliant with NFPA 54, do a draft check on fired equipment after 5 minutes of operation using a smoke pen or light match and blow it out to ensure flue products go up and out. Standards also require completing this check under the worst conditions (for example, with windows and doors closed).
This new, more robust method of checking for the drafts (in the latest edition of NFPA 54) is a game changer for the industry, Puskar says. It’s likely that if testing occurs in the manner currently outlined, many systems will not pass, and deficiencies will need to be addressed. This higher bar for establishing a draft has the potential to save lives.
Finally, don’t forget the basics: Install multiple carbon monoxide detectors, especially if you have air handlers. A CO problem in the equipment room can quickly become a CO problem in the whole facility, as it did in a Beaumont, Texas, middle school in 2016 where nearly 200 students and staffers were sickened when CO generated in a mechanical room was spread throughout the school with an air handler. This incident prompted the state of Texas to require CO detectors in many boiler rooms.
Hazard 3: Neglecting “I Noticed Something” Hazards
A serious gas leak won’t often show up looking like a gas leak, but it will produce what Puskar calls telltale “I noticed something . . .” signs. While these may be “weak” signals, safety professionals should take them seriously, he says.
- Carefully consider repairs to natural gas and fired equipment, as they can be a sign of problems. For example, a weld showing significant signs of corrosion at the bottom of a pressure vessel at the Loy Lange Box Co. was ignored before its bottom patch failed in 2017. The vessel was launched into the air, tumbling through 650 feet of space before landing in a nearby linen company and killing four people.
- Burned spots or burned paint on equipment indicate that refractory has failed. Companies cannot tolerate these conditions or warped panels, Puskar says.
- Process variable instability seen as wide swings on a control chart is a sign that something is wrong.
- Dark gray or black smoke coming out of the stack can indicate a problem with air intake on a burner or a burner damper.
- Don’t rely on smell as an indicator of gas. Those exposed to chronic low levels of the odorant Marcaptan experience odor fatigue and fail to distinguish increasing levels of gas in the room. New piping can make this worse: Until it's completely absorbed, it will not create an odor, a phenomenon called “odor fade.”
- Sounds can indicate problems, too: Lean burners are noisy, and in pipes where steam is accelerating and causing dramatic force, you may hear or even feel a banging called “water hammer.”
Hazard 4: Risks of Equipment Start-Up
Starting up fired equipment carries an extra risk, despite the equipment not being fully fired.
Why? “Every time we try to start, fuel gets released into a firebox — at least 10 seconds of pilot fuel and 10 seconds main flame fuel,” Puskar says. “If we did this a bunch of times and did not get a good purge, with each successive try we would accumulate more of a flammable mixture until we hit the lower explosive limit of natural gas at 4.3%.”
Puskar’s offers a straightforward rule for combatting this: Do not make more than two start-up attempts without time and help. If you’ve tried twice and the equipment hasn’t started, give it a half hour and get help, he says.
Many companies place tags or stickers with QR codes near the equipment with start-up and shut-down procedures as well as troubleshooting tips, daily checklists and more, he says.
Hazard 5: Lack of Communication on Hazardous Jobs
In 2019, multiple explosions occurred at a University of Nevada, Reno, dorm when a contractor replacing a firing valve thought the valve was at a low fire position when it was actually wide open. Fortunately, no one was killed.
It’s an intense near-miss that could have been avoided with a proper hazardous job meeting. Puskar recommends that these meetings address isolation, purging, training, commissioning and an emergency plan, whether you’re working with in-house employees or contractors. To help your efforts, Puskar has created a downloadable template.
Armed with this knowledge, you can prevent the kind of catastrophic incidents Puskar highlighted and keep your workers, facility and even your neighbors safe.
Understanding Risk Management and Assessment
Get the resources and expert guidance you need to improve how you assess risks to prevent hazards, protect workers and safeguard equipment.
Learn more